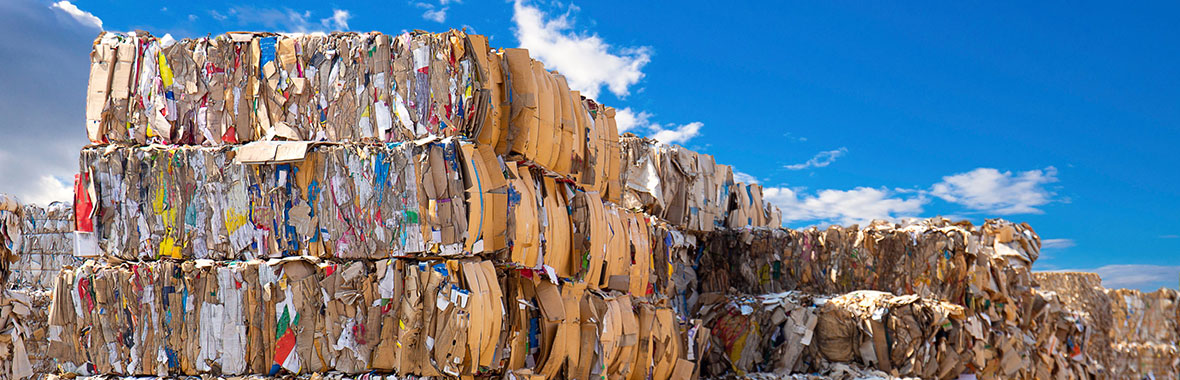
Due to the world energy shortage and environmental pollution problem, people are searching for a reasonable and effective method to solve that problem. So the renewable energy source - biomass energy appeared. That kind of energy can not only be a substitute of traditional fuels, but also protect the environment, which is a kind of perfect energy. Waste paper pellets belong to this kind of energy. You may know that more than 60% of the estimated 17 billion cubic feet of wood felled globally each year is used for paper and pulp. In addition, it should be kept in mind that recycling newspaper saves about 1 ton of wood while recycling print or copy paper saves around 2 tons of wood.
The paper pellets made from paper waste meet the quality requirements of the energy system. Paper pellets has high density and its amount of Btu is similar to coal. Actually, the production cost of paper pellets are relatively low. The biggest cost of paper pellets is the transportation cost. Paper pellets contain less sulfur and produce less carbon monoxide than coal, making them more attractive. Compared to wood, paper has lower levels of formaldehyde. In addition, pelleting from recycled paper can effectively reduce waste at landfills.
Why Paper Recycling is important?
- Worldwide the pulp and paper industry is the fifth largest consumer of energy, accounting for 4% of all the world’s energy use.
- Over 60% of the roughly 17 billion cubic feet of timber harvested worldwide each year is used for paper and pulp.
- The paper industry uses more water to produce a ton of product than any other industry.
- Discarded paper is a major component of many landfill sites, accounting for about 35% by weight of municipal solid waste.
- Seventeen trees and 6953 gallons of water can be saved by recycling just one ton of paper.
How to Make Waste Paper Pellet?
Waste Paper Pellet Plant Production Line Flowchart
Collecting and sorting
Waste papers are abundant in schools, printing companies, market, and office buildings. Paper mill residues are another important source. These materials have different sizes and features, you need to sort them in groups for future processing.
Grinding
You need a hammer mill to crush large size of waste papers into powder with the size of less than 6mm.
Drying
The moisture content of paper materials should be 12%-15%. Neither higher or lower are not acceptable. If the papers are too dry, it would cause static charge and make the pellets light and fluffy. In this regard, you can add certain amount of water to the pellet making machine when processing.
If the moisture content is over-high, you need to lower it by putting the powdery material in a rotary dryer or a pipeline dryer.
Making paper pellets
This is the core process of making paper pellets. Feed materials of proper size and moisture content into the paper pellet machine. They will get compressed and molded in the compression chamber and come out in the shape of cylinders. Usually, there are ring die pellet machine for large-scale production and flat die pellet machine for small-scale production.
Pellet cooling
The newly produced paper pellets has high temperature of 90 ℃. So you need a pellet cooler to lower the pellets to room temperature. Cooling can improve the stability and hardness of paper pellets. Also, you can put the paper pellets in open air for natural withering.
Pellet sieving
Use a sieve to remove the residual powders in the paper pellets. These powders can be re-pelletized together with the left materials.
Pellet packing
Pellet packer is essential for large-scale paper pellet production. It can weigh and package the pellet products in bags. Package can protect the paper pellets from erosion of moisture and wind. Pellets can be stored in the closed silos.
The Benefits Of Paper Pellet
1. Quality: Paper pellets are made to meet the quality demands of the energy system. They are very dense, and the Btu content is similar to coal. The dry processing gives them extremely low moisture content.
2. Cost: The price of paper pellets is one direct benefit and a main lure for customers. Transportation is the highest cost component, therefore, the distance of your industry from the pellet manufacturer may be the biggest determinant of its economic value.
3. Environment: Paper pellets have less sulfur and produce less carbon monoxide than coal, which makes them a little more attractive. Compared to wood, paper has less formaldehyde. Besides, using recycled paper for pellets is effective in reducing landfill waste.
4. Lubrication: Paper pellet dust can lubricate the burning system. It is found that paper pellets absorb some of the moisture on coal, allowing the coal to flow more easily on its way to burning.
Investment Guide
We provide customers with cost-effective solutions that are reliable, professional, affordable and add value to their businesses.