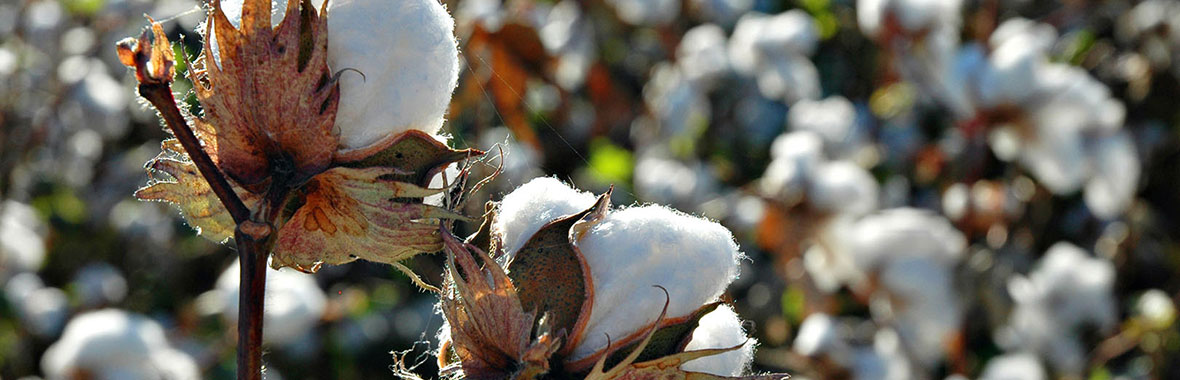
Cotton is the main economic crop, and it occupies about 40% of the global fiber production. The cellulose content is about 87%-90%. The highest production countries of cotton are China, America, India, Pakistan, Egypt, etc. Large production of cotton leaves huge amount of cotton wastes, the main waste is cotton stalks. The stalks are usually 1-2meters, when they are stacked, it will take up a relatively large space.
Abanduant Raw Material
Approximately 80 countries worldwide produce cotton, the U.S., China, and India together provide over half the world’s cotton. Other major producers are Uzbekistan, Pakistan, Brazil, Turkey, Australia, Turkmenistan, Greece, Syria and Egypt.
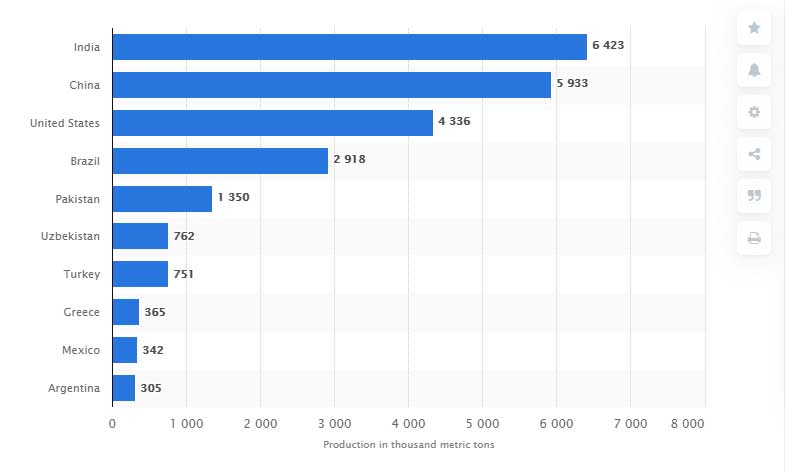
This statistic shows the world's leading cotton producing countries in crop year 2019/2020 (in 1,000 metric tons)
Cotton Stalk Properties
A number of properties are commonly known to affect the success of pelleting, including: heating value, moisture content of the material, density of the material.
High Heating Value
In terms of heating value, heating value ( or calorific value) is essentially a material for burning as fire or as a thermal source of energy. There is a calorific energy analysis in cotton plants could be helpful in developing highly applicable and productive planning for energy policies. The results shows that the calorific energy in different organs of cotton is different. The lowest calorific energy value in all plant organs was observed at leaves(15.955 KJ/g), while seeds contains the highest energy value varied between 22.750-23.078KJ/g. The calorific values of dry cotton stalks are varying from 15.861 to 15.100 KJ/g.
Compared with other crop residues, the calorific energy of wheat straw, rice straw, corn stalk, soybean stalk are 17.98, 17.12-18.68, 15.40-18.25, 21.81-23.01 KJ//g, respectively. Therefore, cotton stalk can be used as pellet fuel in the respect of heating value.
Low Moisture Content of Cotton Stalk
Water is one of the most useful agent that are used both as a binder and lubricant. Therefore water is particularly necessary as an aid in pelletizing. Several investigations of different materials indicate that the strength and density of pellet increase with increasing moisture until an optimal level is reached. The optimal moisture content for agricultural residues to be pelletized ranges between 8-15%. Cotton stalk moisture content is in this range. The stalks are left on the field, thus losing about 80% of their moisture in about 5 days. That means the stalk moisture content reaches the recommended range in a time period of less than one week. This implies that cotton stalks can be pelletized one week after the harvest operation is finished without incurring any additional cost for drying.
High Bulk Density
Bulk density is the ratio between the weight of the pellets and the amount of space they take up. It reflects the amount of solid material packed into the pellet and therefore has a relationship to the heat content of the fuel. Lower bulk density may result in lower conversion efficiency, as it gives rise to poor mixing characteristics and nonuniform temperature distribution, both of which may create unfavorable operating conditions in the thermochemical conversion systems. On the other hand, higher bulk density may result in lower transportation and storage costs and lower emissions during combustion. A good quality pellet will have a density of 650kg per m³. The pulverization of cotton stalk can increase its density to 1080kg per m³.
How to Make Cotton Stalk into Pellet?
The usual pelletizing process includes: crushing, drying, pelletizing, cooling and packing. There are some differences in the cotton stalk pellet production line. Because of low moisture content of cotton stalk, the drying is unnecessary during the whole process, which bring a lot of convenience during production. So the cotton stalk pellets making process is crushing-pelletizing-pelletizing-cooling and packing(if necessary).
Cotton Stalk Pellets can be produced in small scale by a small-scale pellet machine, and also a large capacity pellet making machine can produce large scale cotton pellets. The manufacturing processes that make cotton stalk pellets include grinding as the initial stage, drying, pelletizing, cooling, sieving, and packaging.
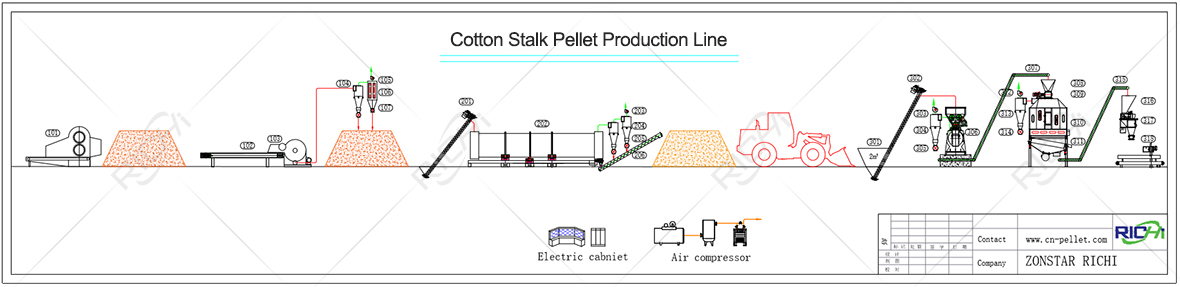
Cotton Stalk Pellet Plant Production Line Flowchart
1. Grinding and Drying of the pellets
This is the first process of cotton stalk pellet production after the cotton harvest is completed. In this process the moisture content on the stalk should not be too low or too high. The proper moistness satisfied is 18% and the minimal level should be 12%. If the moisture content on the stalk is higher than the recommended sawdust dryer can be used to dry the stalks but if moisture content is less than the recommended 18% then there is absolutely no need to go through the drying process. It is very crucial that before the stalks are pelletized the size of the material to be suitable. To crush the stalk into shorter particles the hammer mill is efficient equipment that can be used for the grinding process. And now with the recommended level of moisture in the raw material and the right size the next process of pillarization can take place.
2. Pelletizing and Cooling
This is the second and most important process of the cotton stalk pellet production. Different sizes of machines are used depending on the size of production there is. Larger processing equipment will be used for large quantities of output. There are two different types of fuel pellet machines; the flat die wood pellet mill, which is driven by diesel engine or electric motor and the ring die wood pellet mill. Flat die pellet mill is stress-free to operate and maintain, easy to move from one point to another, is small in size and mostly favored pellet making machine for the lesser scale pelletizing. After the grinding and drying process, the pelletizing process begins with the above named machines. After the material is pelletized they are usually very hot and soft when they leave the pellet machine. Thus it is very important to cool the pellet in the pellet cooler to strengthen and make the pellets durable for the market.
3. Screening and Packaging of the pellets
Now the final stages of making the finest cotton stalk pellets, which are cooled, are passed through a vibrating screen to remove fines. The fines can go through the pelletizing process again and once screened they are ready to be packed and used.
The production of cotton stalk pellets is significant to the farmers as the waste from agricultural produce is turned into a valued product. This improves the economy and offers jobs to the unemployed locals of the community. Producing cotton stalk pellets instead of burning the waste product from the cotton harvest is advantageous because it will prevent burning the waste that causes air pollution, burning will decrease the natural action of the soil which can lead to drop yields and cause soil erosion which is not a good outcome to the farmer.
Comparison between Cotton Stalks and Cotton Stalk Pellets
Investment Guide
We provide customers with cost-effective solutions that are reliable, professional, affordable and add value to their businesses.